ACC Boning Room Upgrade
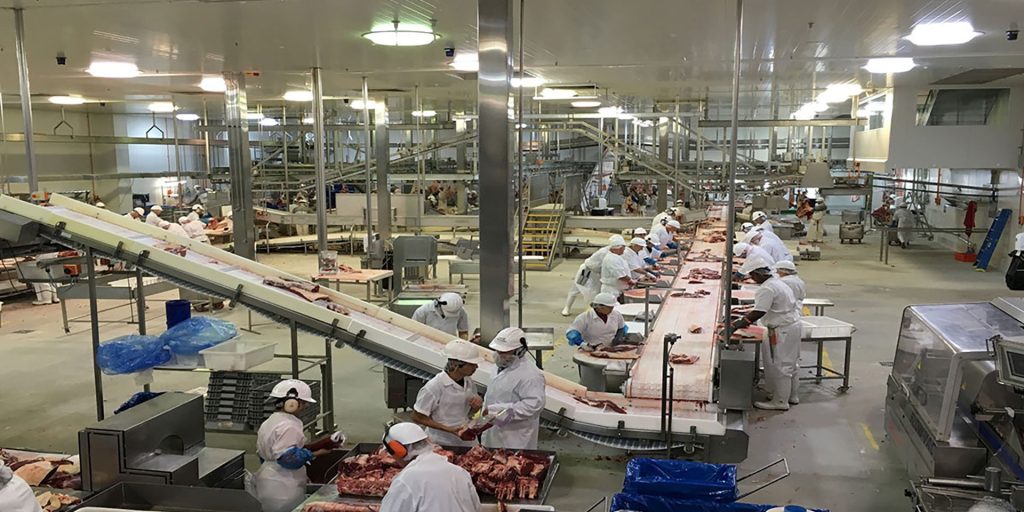
CE Group, an experienced electrical industrial contractor, was engaged to design and construct the installation of electrical services for a new Beef Boning Room. The project was fast-tracked to align with the client’s planned shutdown requirements, with a demanding timeline of sixty days, including just sixteen days to dismantle the existing setup and commission the new facility.
CJ Nutracon Meat and Bone Marrow Processing Plant
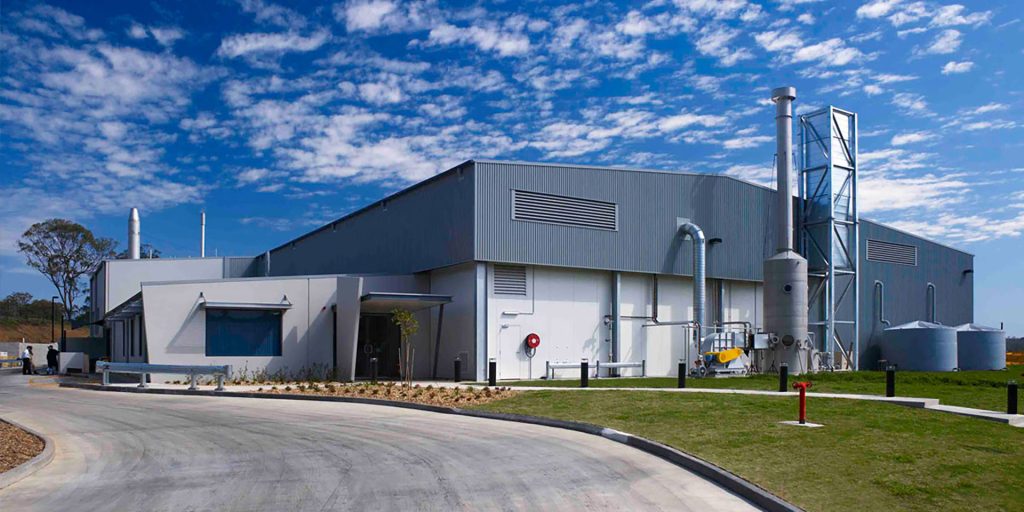
CJ Nutracon is a subsidiary of Korean food manufacturing giant, CJ Cheil-jedang, and manufacture and supply products sourced from the Australian food, meat and livestock industries, specialising in the manufacture of enzyme hydrolyzed beef extract, beef leg bone extract and other meat extract products. The project also houses the on site laboratory.
The Toowoomba plant is the result of a relocation of the Oklahoma, USA facility, which was closed down as a result of the mad cow disease in the USA.
JBS Hide Processing Facility
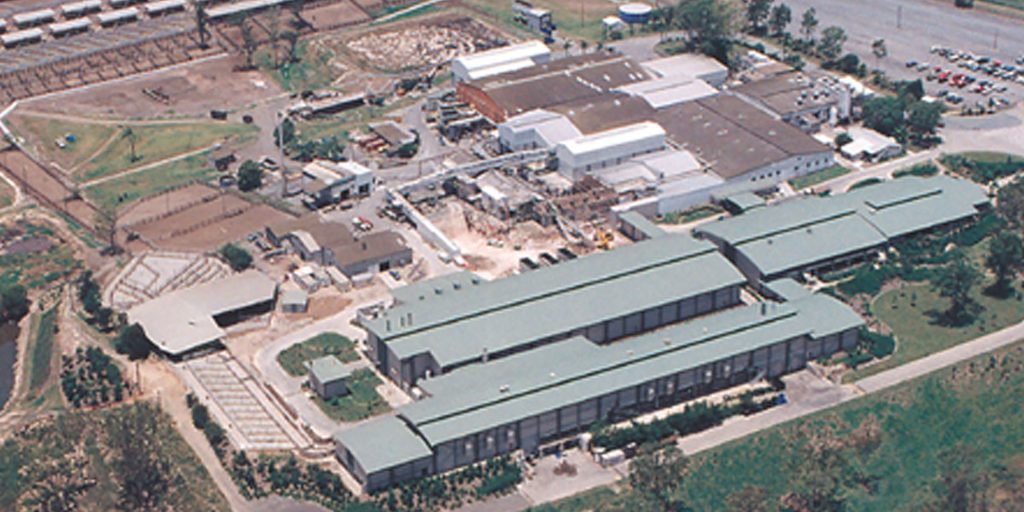
JBS Australia Pty Limited is a division of JBS, Brazil’s largest multinational in the food sector, and the worlds largest meat company.
JBS Australia’s objective was to create an environmentally sound Hide Processing Facility, allowing them the ability to process hides in-house and continue to meet their ever-increasing supplier demand. This required redesigning their entire process from the ground up.
KPC Carcass Conveyors
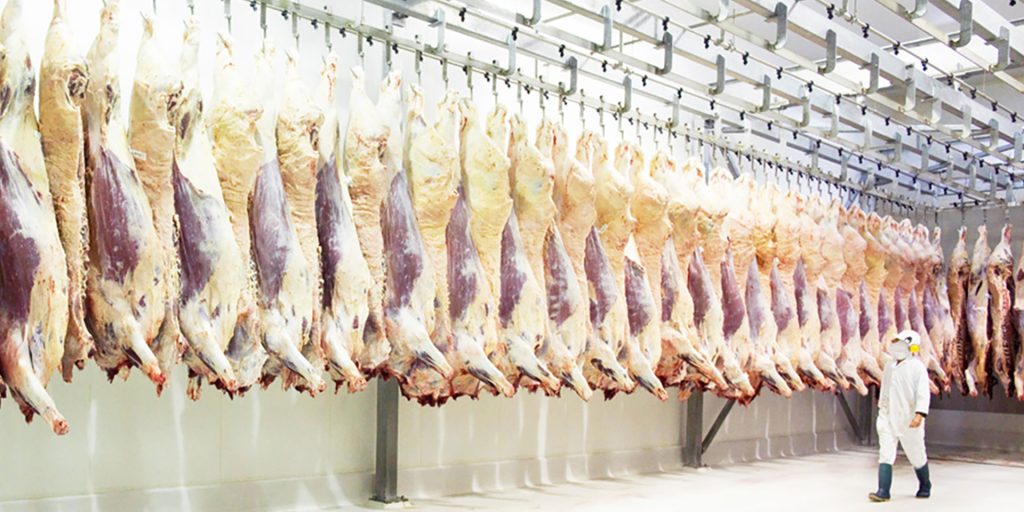
CE Group, a leading electrical industrial contractor, was engaged by Kilcoy Pastoral Company (KPC) to deliver a comprehensive, turn-key electrical solution for the Carcass Conveyor system.
Primo Smallgoods Refrigeration
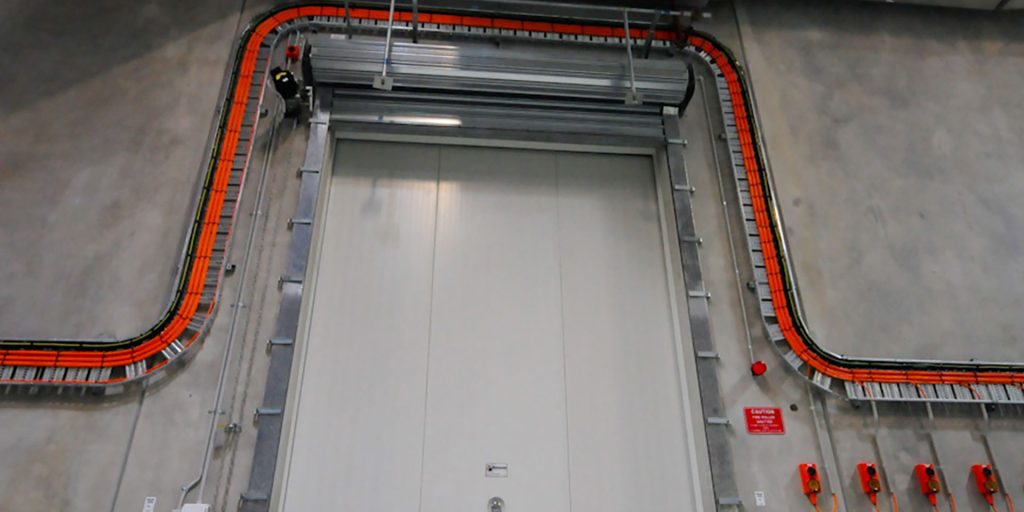
CE Group, a leading electrical industrial contractor, designed and manufactured the motor control centers (MCCs) for two main Refrigeration Engine Rooms. Additionally, they developed various field MCCs and Variable Speed Drive (VSD) panels for the Control Refrigeration Penthouses and Evaporation Plant.
Primo Smallgoods
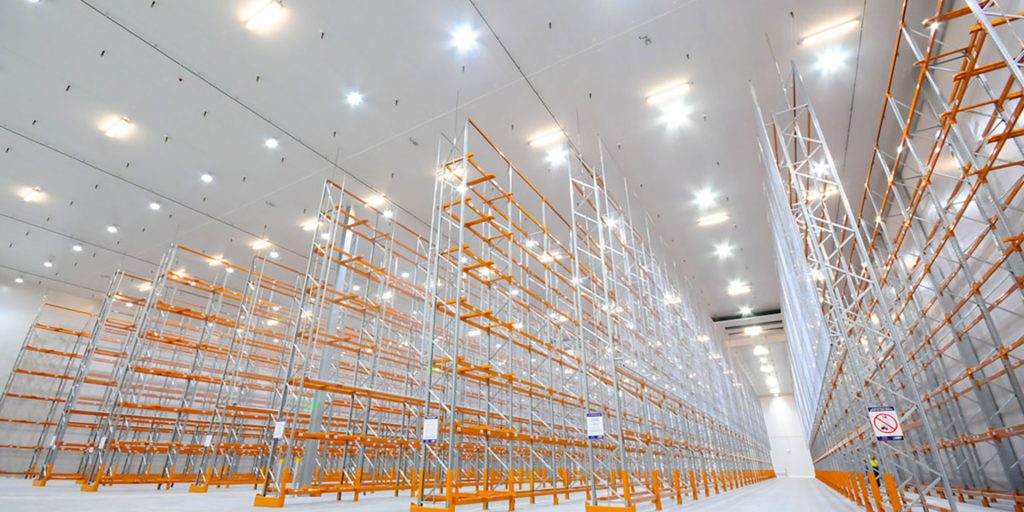
As an experienced electrical industrial contractor, CE Group was tasked with developing an efficient electrical distribution system to meet the challenge of the dual-building layout. In addition, smart switchboard location planning, distributed control systems, and advanced drive technology were essential factors in ensuring the project’s success.
JBS Townsville Kill Floor
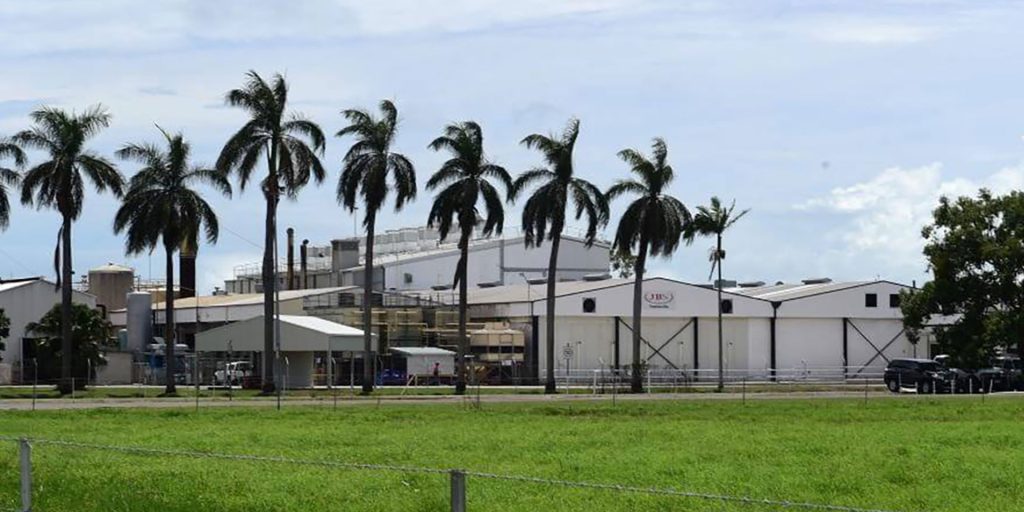
CE Group was engaged by JBS Australia to provide a turn-key solution for replacing and upgrading the existing Motor Control Centre for JBS Townsville’s Kill Floor operation.
The scope of works included designing a solution for consolidating and upgrading the PLC and Motor Control equipment from separate areas of the plant, into one Motor Control Centre for ease of maintenance.
Schweppes Wulkuraka Facility
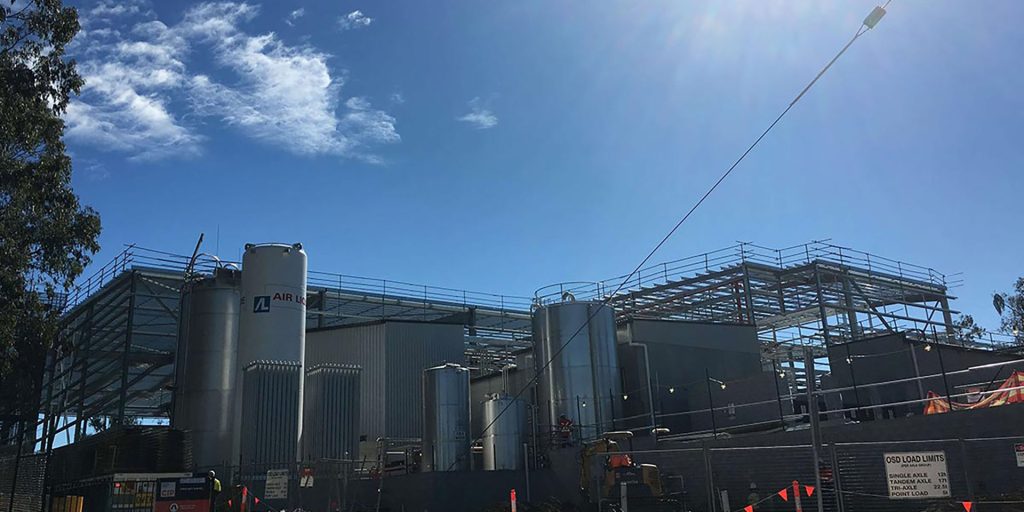
CE Group, an experienced electrical industrial contractor, was engaged to provide general light and power systems for the extension of a Production and Distribution facility in Ipswich, QLD. This project included delivering electrical solutions for various critical production areas, such as Syrup and Post-mix facilities, as well as Flammable and Dangerous Goods Storages. Additionally, CE Group provided electrical services for refurbished office spaces, ensuring all areas were fully operational.
To accommodate the facility’s upgrade, the existing site transformer was decommissioned. In its place, two new 2500A Main Switchboards were installed, both fed by newly installed 1500kVA Transformers. This complex installation required precise planning to ensure a smooth transition. The existing facility was reconnected to the upgraded Main Switchboards during a carefully programmed, seamless changeover period. This allowed ongoing operations to continue without interruption.
Furthermore, CE Group was tasked with adhering to a challenging project timeline, which required minimizing disturbances to the existing operations at the facility. As a result, close coordination and communication were essential to the project’s success. The CE Group team worked extensively with all service providers, ensuring the integration of the new systems was both smooth and efficient.
Throughout the project, CE Group demonstrated its expertise as a trusted electrical industrial contractor by effectively managing both the technical and logistical aspects of the installation. Their ability to deliver on time, while minimizing disruptions, contributed significantly to the overall success of the facility’s extension.
In conclusion, the extension of the Production and Distribution facility highlights CE Group’s capabilities in delivering tailored electrical services for industrial projects. By maintaining a strong focus on project timelines, seamless integration, and operational continuity, CE Group solidified its reputation as a reliable electrical industrial contractor in the industry.
Teys Beenleigh WWTP
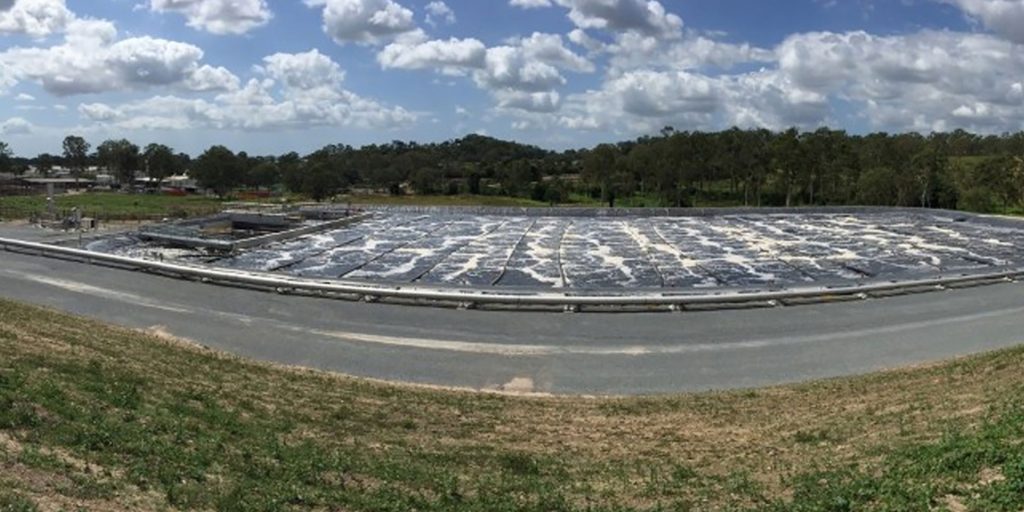
CE Group and Teys Australia continued with the Beenleigh Waste Water and Bio-Gas Collection project. As a trusted electrical industrial contractor, CE Group was tasked with upgrading the wastewater treatment system at the Teys Beenleigh facility.
JBS Dinmore Lighting

CE Group’s Scope at JBS Dinmore was to replace all the lights in the ceiling, above the Boning Room Floor. The JBS Dinmore Processing Plant is the largest beef plant in the Southern Hemisphere, with a daily production of 3,400 heads per day and an onsite staff base of more than 2,000 team members.
All work for this project was completed during weekend shutdowns, due to the tight timeframes for completion and difficult working conditions during business hours.