Dalrymple Bay Coal Terminal (DBCT) Stacker Project
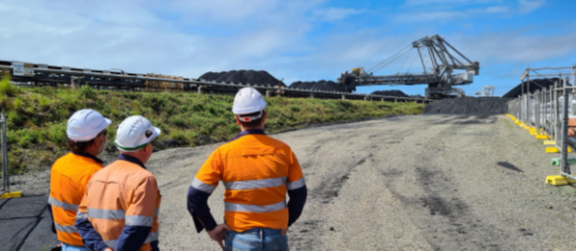
Dalrymple Bay Coal Terminal, a critical part of Queensland’s coal export infrastructure, is undergoing a significant upgrade to sustain its operational efficiency. As part of this effort, the terminal is replacing its existing rail-mounted stacker machine (ST1) with a newly designed Stacker (ST1A). This upgrade is essential to improve the terminal’s capacity and enhance its long-term reliability.
BMA Goonyella Riverside Mine Dewatering Screens Upgrade
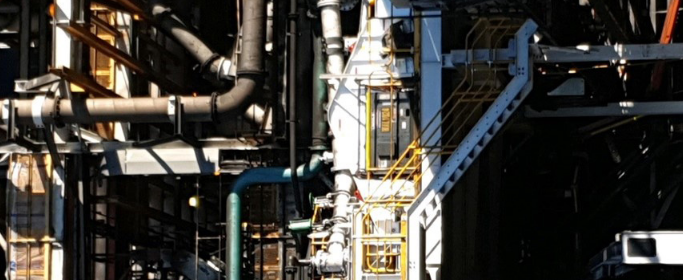
Goonyella Riverside Mine (GRM), a key coal mining operation in the Bowen Basin, is located about 30km north of Moranbah and 190km southwest of Mackay. As a leading electrical mining contractor, CE Group was engaged to upgrade the mine’s Coal Preparation Plant 1 (CPP1) Fine Rejects Dewatering system. This project aimed to rectify a plant bottleneck, increasing production rates and improving system reliability.
The upgrade involved replacing the existing dewatering screen with larger dual screens. This enhancement was critical to addressing a single point of failure (SPF) within the system, which previously halted production when unavailable. By upgrading the system, the mine would not only boost productivity but also ensure redundancy, a key requirement for uninterrupted operations.
As part of this major SMP (Structural, Mechanical, and Piping) and Electrical & Instrumentation (E&I) overhaul, CE Group undertook a wide range of services. These included the supply and installation of new Motor Control Center (MCC) cells, crucial for ensuring the safe and efficient operation of various electrical systems. Additionally, CE Group handled the supply and installation of all pneumatic equipment, power and control cabling, and instrumentation across the site.
The project also required the installation of remote I/O panels and remote local control stations, enhancing the mine’s operational efficiency. These installations allowed for better control and monitoring of key systems, ensuring that production could continue smoothly without unnecessary interruptions.
Throughout the project, CE Group’s extensive expertise as an electrical mining contractor played a vital role in delivering high-quality results. The team worked closely with key stakeholders to ensure the project was completed on time and within budget, all while maintaining strict safety standards.
This successful collaboration at Goonyella Riverside Mine further solidifies CE Group’s reputation as a trusted electrical mining contractor. Their ability to manage complex electrical and instrumentation projects in challenging mining environments ensures that clients can achieve improved operational outcomes while maintaining safety and efficiency.
As a leading electrical mining contractor, CE Group was engaged to upgrade the mine’s Coal Preparation Plant 1 (CPP1) Fine Rejects Dewatering system.
Ammonium Nitrate Storage Bins – Bard Engineering
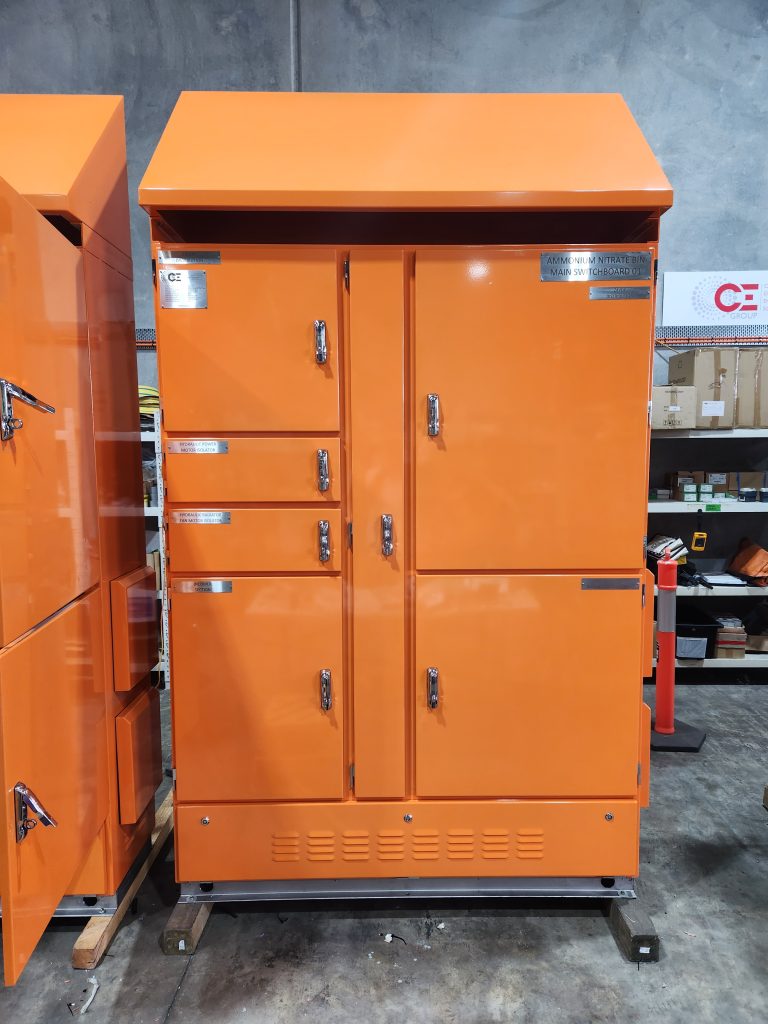
CE Switchboards, a trusted switchboard manufacturer, was engaged by BARD Engineering to design, manufacture, and supply two 400Amp outdoor main switchboards for ammonium nitrate storage bins.
Goonyella Riverside Mine Switchroom Prefab & Install
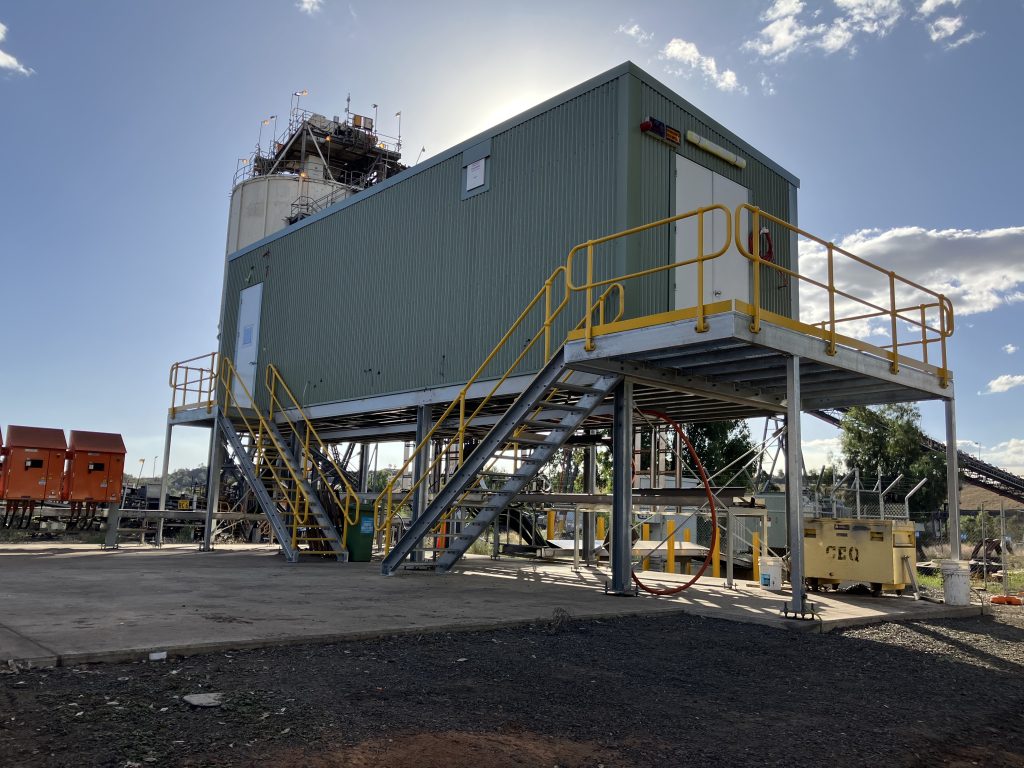
CE Group undertook the design, manufacture and supply of BHP specified RV Switchroom
Hail Creek Industrial Area Upgrade – Warehouse
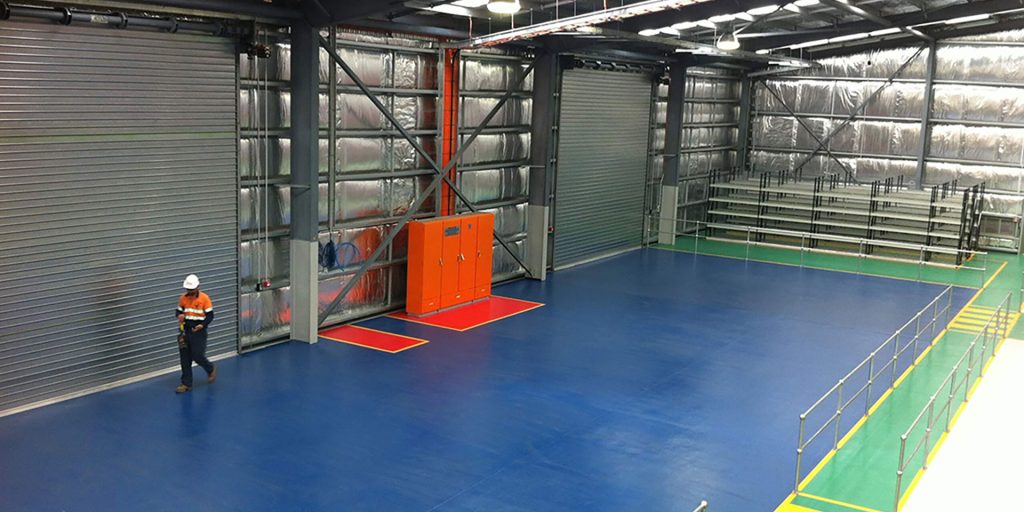
The Hail Creek IAU – Warehouse project saw CE Group continue its support of the Mining Industry. The project involved the supply, installation, testing and commissioning of electrical works for the 2.750m2 warehouse at Hail Creek Mine .
ACC Boning Room Upgrade
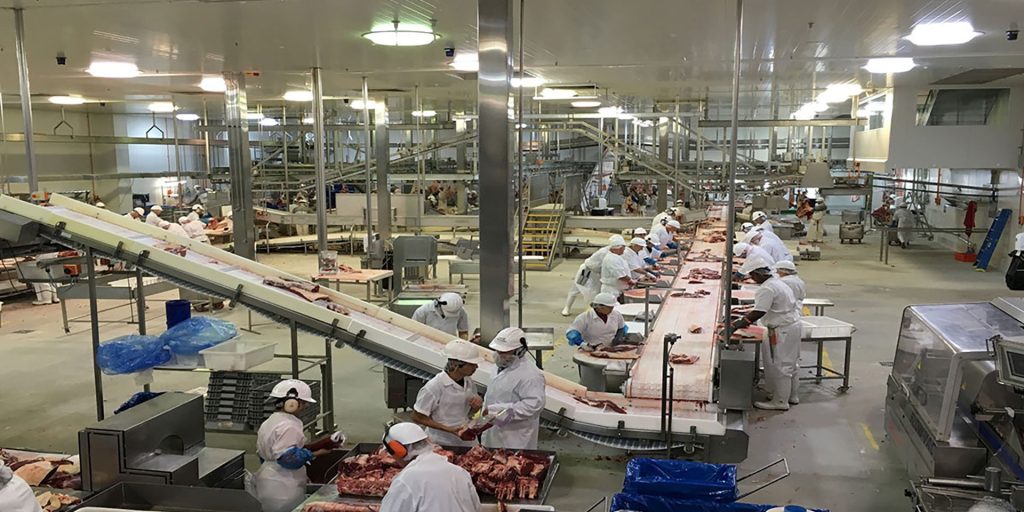
CE Group, an experienced electrical industrial contractor, was engaged to design and construct the installation of electrical services for a new Beef Boning Room. The project was fast-tracked to align with the client’s planned shutdown requirements, with a demanding timeline of sixty days, including just sixteen days to dismantle the existing setup and commission the new facility.
CJ Nutracon Meat and Bone Marrow Processing Plant
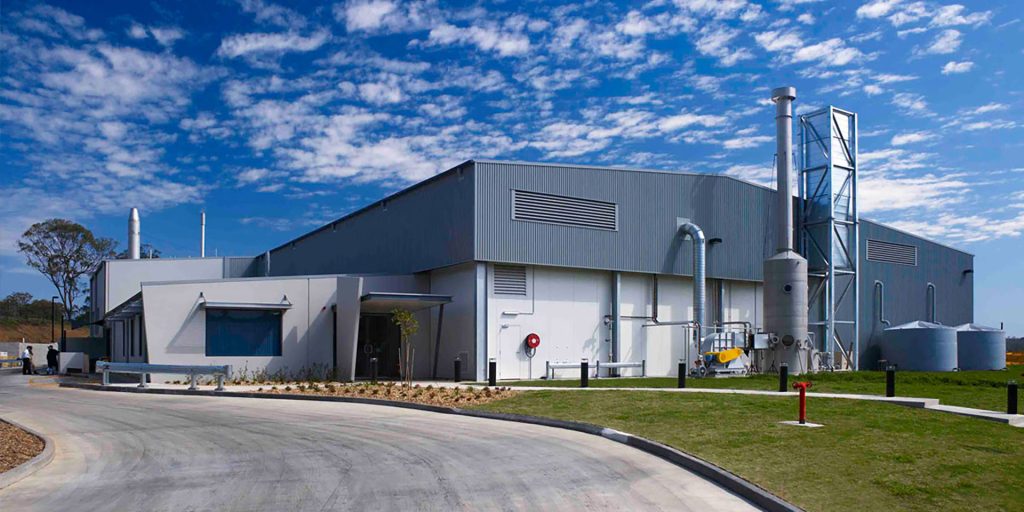
CJ Nutracon is a subsidiary of Korean food manufacturing giant, CJ Cheil-jedang, and manufacture and supply products sourced from the Australian food, meat and livestock industries, specialising in the manufacture of enzyme hydrolyzed beef extract, beef leg bone extract and other meat extract products. The project also houses the on site laboratory.
The Toowoomba plant is the result of a relocation of the Oklahoma, USA facility, which was closed down as a result of the mad cow disease in the USA.
JBS Hide Processing Facility
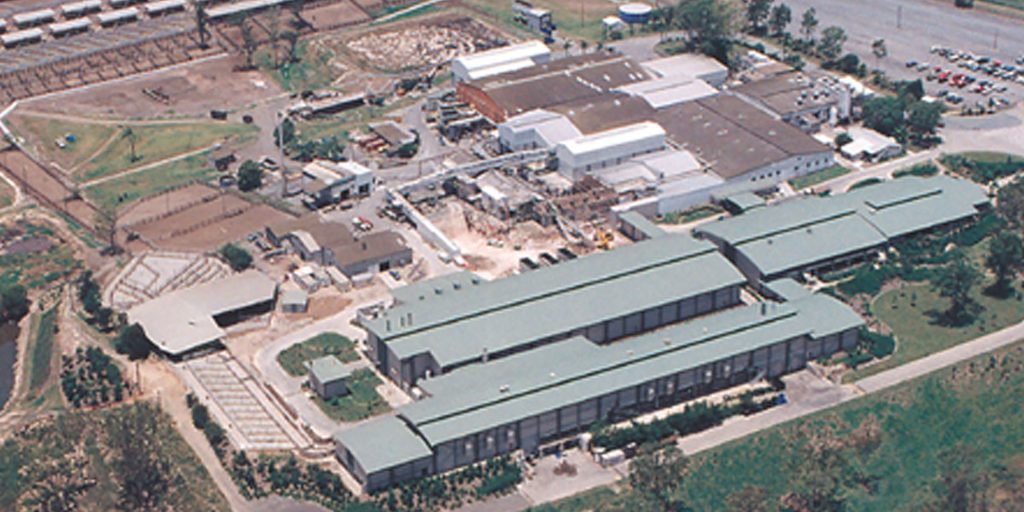
JBS Australia Pty Limited is a division of JBS, Brazil’s largest multinational in the food sector, and the worlds largest meat company.
JBS Australia’s objective was to create an environmentally sound Hide Processing Facility, allowing them the ability to process hides in-house and continue to meet their ever-increasing supplier demand. This required redesigning their entire process from the ground up.
KPC Carcass Conveyors
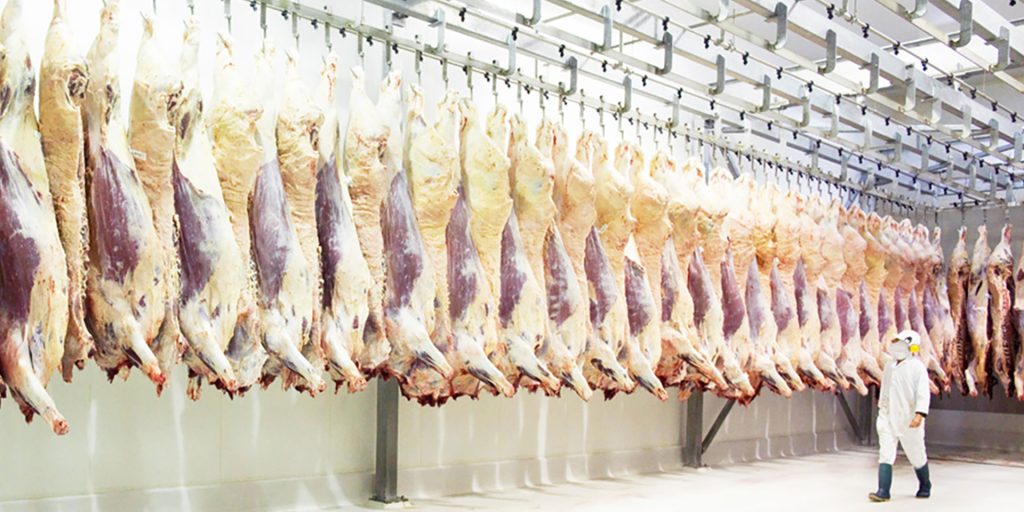
CE Group, a leading electrical industrial contractor, was engaged by Kilcoy Pastoral Company (KPC) to deliver a comprehensive, turn-key electrical solution for the Carcass Conveyor system.
Primo Smallgoods Refrigeration
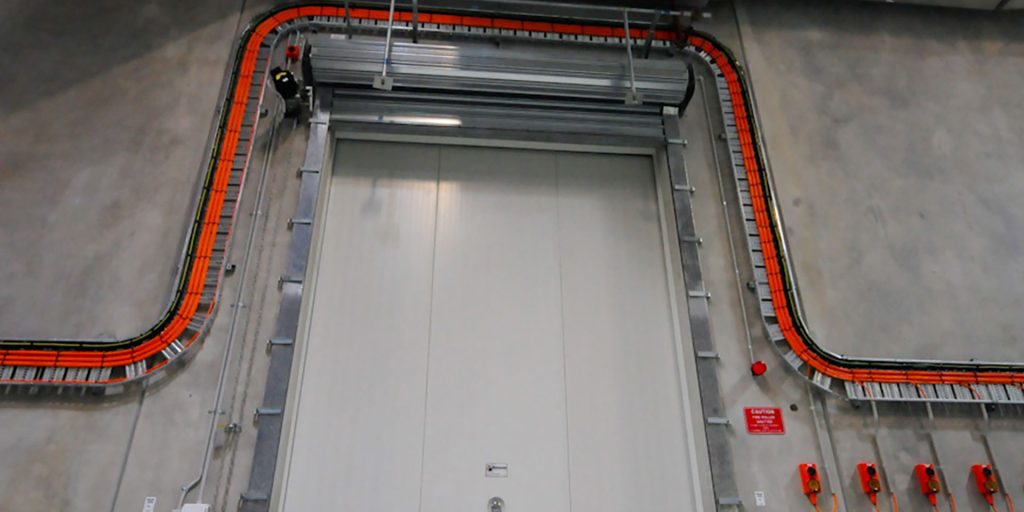
CE Group, a leading electrical industrial contractor, designed and manufactured the motor control centers (MCCs) for two main Refrigeration Engine Rooms. Additionally, they developed various field MCCs and Variable Speed Drive (VSD) panels for the Control Refrigeration Penthouses and Evaporation Plant.